Creating Your Part
Here we outline the typical path SST follows when creating your hermetic parts. We begin with an engineering review and follow precise steps all the way to final inspection. This process is typical of parts involving a ceramic-to-metal seal. But custom builds, parts using other materials, and/or special requests may require some different steps.
1) Engineering Review and Assessment
SST designs and manufactures a range of hermetic products including hermetic feedthroughs, connectors, isolators, viewports, and various air-side and vacuum-side accessories. The basis of the majority of these products is ceramic-to-metal sealing and/or glass-ceramic sealing. The process starts with a comprehensive review of engineering and contract requirements that ensures SST has a complete understanding of the customer’s application and service needs.
2) Custom Feedthrough Design
Is your part a standard catalog entry? Or do you need a custom feedthrough design? This is the most significant consideration when determining the timing requirements for your project. SST views parts in three common ways. First, our standard catalog parts can be ordered as is, according to our provided technical drawings. Next up are modified standard parts, which are parts with small changes, like a shorter conductor, that do not significantly affect engineering or production time. And then we have totally custom feedthrough designs. It is important to consider engineering time at the onset of your project if a unique part is required.
3) Material Sourcing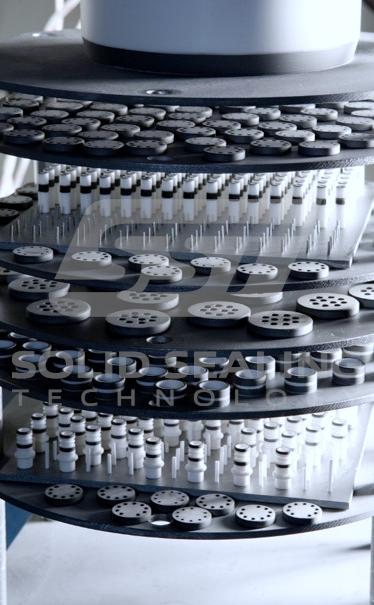
Following the design approval is the sourcing phase. SST identifies the specific materials and components needed to produce each customer’s part. We work with an extensive supplier base to acquire ceramics, machined metals, formed metals, precious metal braze alloys, and accessory connectors. Lead times for these components can range from 5-12 weeks and will drive the overall production time.
4) Preparation and Metalizing of Ceramics
Manufacturing begins with application of a thick-film molybdenum-based metalizing coating onto the ceramics in locations where joining will occur. This is how the ceramic-to-metal seal begins. The coating is applied either by brushing, dipping, or screen printing. The metalizing layer will be sintered in a hydrogen furnace at a temperature of approximately 1500°C. The film thickness is measured using a calibrated XRF as a quality check. The metalizing process is finalized by electroless nickel-plating the coated areas. The total ceramic preparation process will take roughly ten working days. It is important to note that parts using glass or glass-ceramics do not require metalizing.
5) Mechanical Assembly and Fixturing
The metalized ceramics are then issued to a work order with the appropriate metal components. All of these components will be assembled per print by trained operators. Braze alloys melt into place in the proceeding operation creating the hermetic seals. In many cases, very complex fixturing is required to hold the components in their proper location.
6) Brazing and Furnace Cycles
The assembled components (along with the fixturing) are placed in a brazing furnace where the braze alloys will melt and fuse the associated components together. The brazing temperatures range from 800°C to over 1200°C. A typical cycle time for a braze furnace is 3-4 hours. SST has many types of brazing furnaces including:
- Vacuum furnaces
- Hydrogen furnaces
- Inert gas furnaces
7) Leak Testing
Solid Sealing Technology guarantees leak-free parts for aggressive environments. Our quality and inspection teams leak-test every part we produce with a high-sensitivity helium mass spectrometer. Parts are tested pass/fail to a leak rate of less than 1x10-10 atm.cc/sec.
8) Secondary Manufacturing Services
Common secondary manufacturing services that may be used for more complex custom assemblies include machining and welding operations. Machining helps achieve tight tolerances on brazed parts or prepare brazed assemblies for subsequent welding. SST takes advantage of both manual and CNC equipment to customize parts in our machine shop.
Welding is often the preferred method for adding components to brazed assemblies. Typical applications include adding custom flanges as mounting solutions or adding threaded adapters and contacts for connector solutions. SST has Laser, TIG, and Spot-welding expertise. SST can also laser-mark and serialize parts.
9) Final Inspection and Testing
Final inspection and testing are very important to our customers. SST verifies all critical requirements before shipping, and our customer service team ensures customers have the resources to meet their needs. SST offers vacuum-bagging and other special packaging options if needed. Parts will arrive clean and ready to use out of the box.
Calibrated tools, vision systems, and a CMM are used to verify mechanical attributes. And electrical requirements are validated with the latest electrical test equipment. SST is certified compliant to ISO9001:2015 and often works within the more stringent requirements of defense and medical customers.
10) Delivery of Your Vacuum Feedthroughs, Hermetic Connectors, and Other Products
SST's customer service team works with customers along the way to ensure shipping and delivery meet your requirements. We will use the most effective shipping method and carrier unless a specific option is named by our customers. If you have any questions related to your delivery, please contact us.